MDL Multidaylight Line 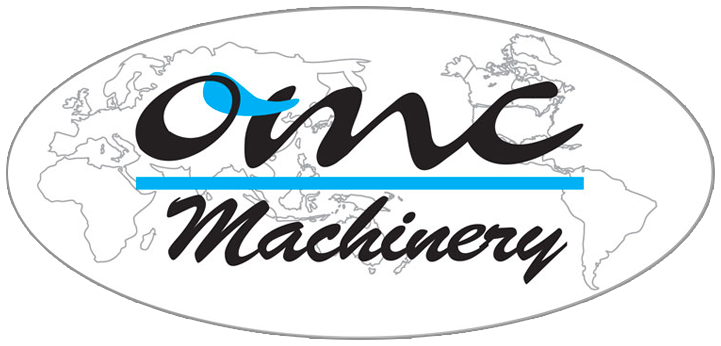
The MDL MULTIDAYLIGHT lines can simultaneously press multiple panels/doors thanks to a loading system with automatic elevator that is able to simultaneously enter multiple panels/doors into multiple daylights.
The MDL Multidaylight lines can be equipped with a single multi-daylight press or even with two independent presses one on top of the other, in order to achieve very high production volumes.

Applications
- Coating panels/doors with veneer/laminate;
- Gluing of honeycomb door elements.
Typical Final products
- Veneered / laminated doors / panels;
- Honeycomb doors.
Accessories / Options
The MDL Multidaylight automatic lines can be equipped with the following accessories:
- Working stations to be installed before the loading elevator for the assembling / gluing of doors and / or panels, for example: platform with pusher (or robot with suction cups bridge), brushing machine, glue spreader, disc conveyor, positioner, lay up table with 90 ° transfer device etc;
- Motorized roller conveyor with 90 ° transfer device after the loading elevator, to get the doors / panels onto the cooling system;
- The cooling system receives the pressed doors / panels from the roller conveyor and lifts them up in a wide circle and then gently lays them on another motorized roller table. During the rotation the doors / panels have enough time to cool down and become ready for the next operation;
- Additional roller conveyor with 90° transfer device after the cooling system, with automatic centering device, to transfer of the doors/panels to other possible stations;
- Suction cup bridge or robot for palletizing.
Model MDL Multidaylight
Modelli e tipi di carico
- 2 +2: Manual loading on automatic loading elevator;
- 3 +3: Manual loading on automatic loading elevator;
- 4 +4: Manual loading on automatic loading elevator.
Loading
The operator manually loads doors / panels, one at a time, onto the feeding belts of the loading elevator: each time a door/panel is loaded, the operator presses the dedicated button and the elevator rises to reach the loading height of the press platens (OMC can also provide an automatic gluing + loading system, upon request). Once the previous pressing cycle is finished, the motorized feeding belts of the elevator automatically transfer the doors / panels onto the press platens (both on the upper and lower set of platens); at the same time the belt of the lower platens of the press rotate to receive the new doors / panels and the doors/panels are unloaded from the press onto the unloading elevator.
While the doors are being pressed, the operator can load new doors/panels to be pressed on the elevator.
Unloading
The unloading elevator is equipped with rollers and TAPES to allow for a uniform cooling of the pressed materials.
The unloading elevator is synchronised with the loading elevator: when the press platens open, a new set of doors/panels enters the press, while the doors/panels that have just been pressed are taken out of the press onto the unloading elevator. (If necessary due to special production requirements, the unloading of the doors from the press onto the unloading elevator can be activated independently of the loading system).
Useful dimensions and hydraulic thrust
- 25/13: 2500×1300 mm, 3 – 4 Kg/cm2;
- 30/13: 3000×1300 mm, 3 – 4 Kg/cm2;
- 35/13: 3500×1300 mm, 3 – 4 Kg/cm2.
The two sets of press platens are independent and can be programmed with different parameters for dimensions, pressing time, hydraulic thrust, cylinder exclusion etc. For instance, while one press is processing small-sized workpieces that require low pressure, the other press can process large-sized pieces with high pressure; this versatile mode allows to increase production volumes according to customers’ needs.
Standard equipment
- Loading elevator with feeding belts;
- No. 2 multilight presses;
- Hydraulic pre-filling system;
- Conveyor belts installed around the lower press platens;
- Digital “Touch screen” panel + PLC;
- Heating system with diathermic oil;
- Unloading elevator equipped with rollers and tapes for the cooling of the pressed material.








