Automation of the PL series 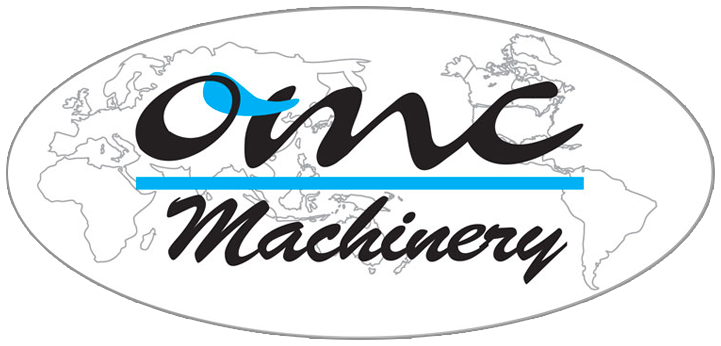
If fitted with additional units and devices, the standard PL presses can be made automatic to increase their potential and achieve the following:
- increase of production volumes;
- production of blockboard panels (edge glued panels);
- multifunctionality;
- incorporation in complete lines.
PLA





The PLA model is a through feed press that offers the following advantages:
- Reduction of production times thanks to its semi-automatic mode (loading activated with a foot switch, automatic pressure, automatic unloading synchronized with the loading of the next workpiece);
- Possible incorporation in an articulated line thanks to the “through feed cycle”.
Applications:
Gluing of veneer and laminate on MDF or chipboard.
Advantages:
Reduction of production times: thanks to the infeed table, the press conveyor belt and the unloading table, the operator, after loading a workpiece, can immediately start preparing the next panel / sandwich to be pressed.
The PLA model includes the following units:
1) loading table, equipped with PVC belt, inverter and foot switch: once the load is ready, the operator presses the foot switch and activates the PVC belt that feeds the panel into the press.
2) Standard press equipped with an additional system of motorized chains + gearmotor + inverter + conveyor belt installed on the lower platen.
The chain system is synchronized with the loading table: as the loading table is activated, the conveyor belt of the press rotates and receives the workpiece into the press.
An air blowing system, installed on the lower platen, creates an air cushion between the platen surface and the conveyor belt to reduce the friction and facilitate the sliding of the belt.
3) unloading table with idle wheels
Once the pressing cycle is finished, the press opens and the panels are automatically unloaded by the conveyor belt of the press onto the outfeed table with idle wheels.
The press is also equipped with a “touch screen” control panel through which the operator can manage all the functions of the pressing cycle.
The PLA model can also be supplied with infeed into the short side.
PL/CsL model
The PL/CsL model is equipped with the unloading system on the same side as the loading table.




PL.lsm
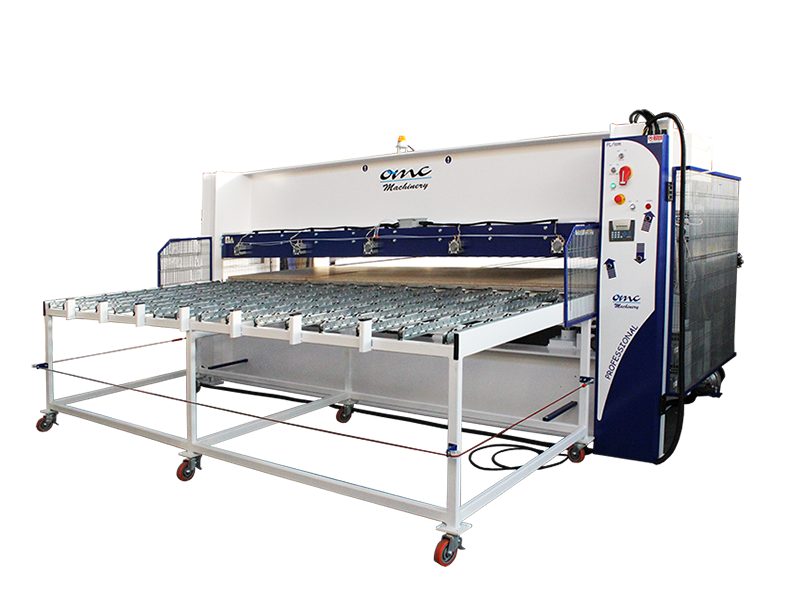
Applications:
The PLlsm press can perform two different operations:
- Coating panels with veneer and laminate: the operator needs to remove the unloading table with idle wheels, manually load the workpieces and exclude the horizontal pressing cylinders;
- Production of blockboard panels (edge glued panels).
Useful dimensions:
- 25/13: 2500×1300 mm;
- 30/13: 3000×1300 mm;
- 35/13: 3500×1300 mm;
The dimensions can be customized according to customer’s needs.
Standard equipment:
- Vertical hydraulic cylinders;
- Horizontal hydraulic cylinders;
- Stop bar to counteract the thrust of the horizontal cylinders;
- Automatic loading table with pushing device and foot switch;
- Unloading table with idle wheels;
- Pneumatic cylinders to facilitate the detachment of the material;
- Digital “Touch screen” panel + PLC;
- Heating system with water or oil boiler.
Options:
- Height adjustment of the front pressing plates;
- Shims to increase the thickness of the front pressing plates;
- Pressing cylinders installed on the short side;
- Downstroke;
- Setup for High Frequency Generator;
- High Frequency Generator.



PL Conversion S3 and PL Conversion S5
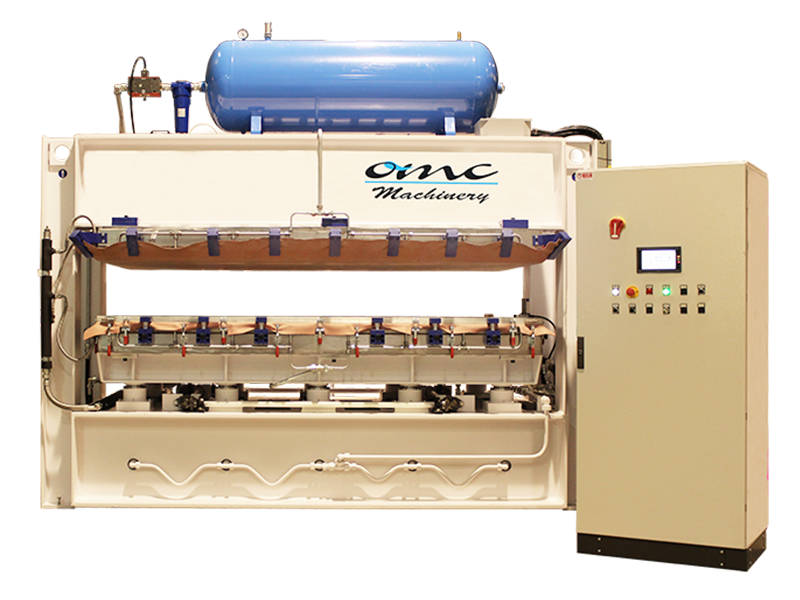
These models are equipped with one or two membranes, for the application of 3D thermoforming films or veneer to coat one or both sides of the workpieces.
These presses can also be used as standard hot/cold presses to coat workpieces with veneer and laminate.
Models:
The press model “PL Conversion S3”, with manual loading, can be used in three different ways:
- As a Cold press;
- As a Heated press;
- As a membrane press to apply PVC and veneer on one side of the workpiece.
The “PL Conversion S5”model with manual loading, can be used in five different ways:
- As a Cold press;
- As a Heated press;
- As a membrane press to apply PVC and veneer on shaped surfaces on one side of the workpiece;
- As a membrane press to apply PVC and veneer on shaped surfaces on both sides of the workpiece
- As a membrane press to apply glossy PVC thanks to the additional “high gloss system” (intermediate flange).
Useful dimensions and thrust:
- 25/13: 2350×1180 mm, Kg/cm2 6 + 1;
- 30/13: 2850×1180 mm, Kg/cm2 6 + 1.
Standard equipment:
S3 model:
- No. 1 rubber membrane;
- Heating system with diathermic oil;
- No. 1 proportional control valve + 500 litre air tank;
- No. 1 vacuum pump with 500 litre tank.
S5 model:
- No. 2 rubber membranes;
- Heating system with diathermic oil;
- No. 2 proportional control valve + 500 litre air tank;
- No. 1 vacuum pump with 500 litre tank.



