PL series press 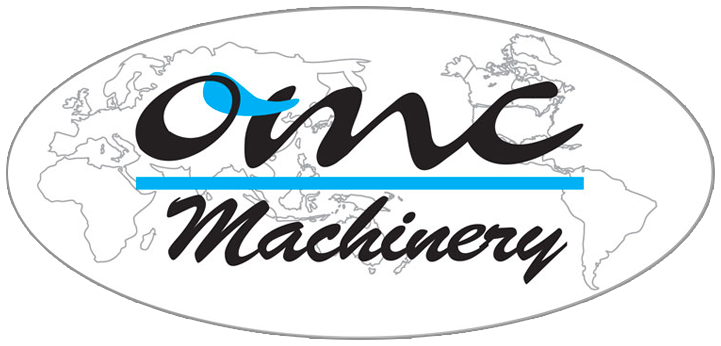
The PL standard presses have been specifically designed to coat MDF or chipboard panels with veneer or laminate; the PL models are typically used by craftsmen, carpenter’s workshops and small/medium sized companies of the wood processing sector.

Standard dimensions:
2500×1300 mm;
3000×1300 mm;
3500×1300 mm.
The standard dimensions can be customized according to customers’ needs.
Types of platens
Assembled platens with coil and aluminum covering
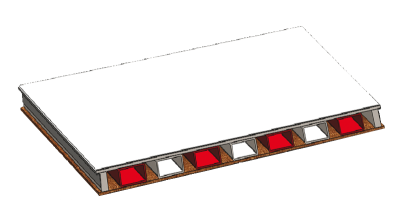
Maximum working temperature 120°C
Maximum working pressure: 3÷5 kg/cm²
The assembled platens are manufactured in our own metal workshop; the coils are coated with a 3 mm thick metal sheet; the platens are covered with an aluminum sheet that provides an excellent surface finish and a very effective heat spreading performance.
Solid steel platens:
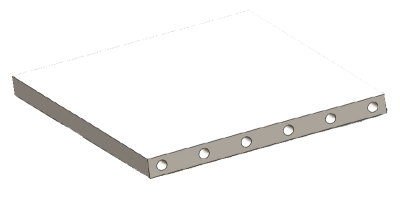
Typical working temperature 120°C;
Maximum working pressure: 30 kg/cm²;
The solid steel platens are manufactured in our own metal workshop with numerically controlled machines; the platens are made of steel plates drilled with holes for the water/oil circulation.
The surfaces can be covered with Mylar or Vetroteflon (for temperatures above 120°C).
Electric platens
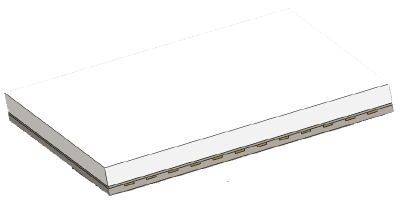
The platens are made of a chipboard base and an aluminium plate that contains the electrical resistors.
Maximum working temperature: 120°C.
Upon request the platens can be supplied with an anodized surface for greater wear resistance.
Assembled and milled platens
(for special applications)
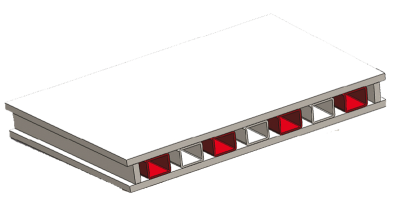
Maximum working temperature: 120°C;
Maximum working pressure: 5÷10 kg/cm²;
The assembled and milled platens are manufactured in our own metal workshop and polished with CNC machines to a standard roughness of Ra 1.6 µm.
The coil is coated with an 8 mm thick metal sheet, which is assembled as a sandwich using a nail welding system.
The platens are coated with a sheet of aluminum or stainless steel that provides an excellent surface finish and a very effective heat spreading performance.
Types of heating systems
Water boiler
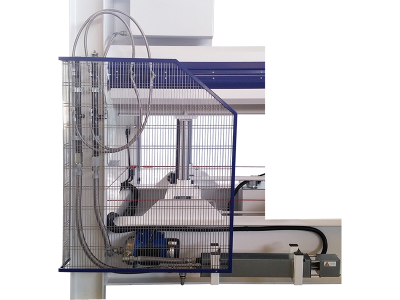
Heating fluid: water
Maximum fluid temperature: 85°C
Heating time: 40 min
insulation: MDF
Type of pipes: flexible, made of rubber
The heating system consists of an electric boiler manufactured by OMC Machinery, a water recirculation pump, rubber pipes and MDF insulation to reduce heat loss.
Oil boiler
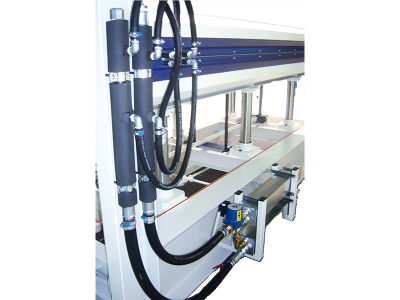
Heating fluid: diathermic oil with 32 cSt viscosity;
Maximum standard oil temperature: 120°C
Heating time: 50 min
Protections: safety nets around boiler and pipes
Type of pipes: flexible, made of stainless steel
The heating system consists of an electric boiler manufactured by OMC Machinery, a water recirculation pump, steel pipes and MDF insulation layer to reduce heat loss.
Cartridge resistors
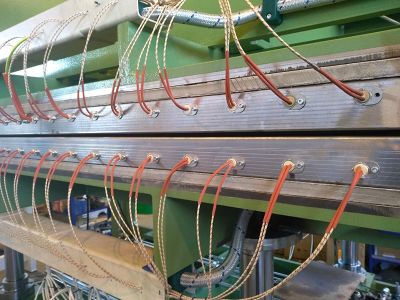
The maximum temperature is customizable according to customers’ needs.
Control panel
The standard panel is equipped with a pressure gauge.
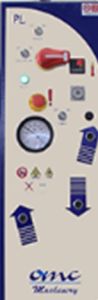
The press can also be fitted with a digital “Touch Screen” control panel.
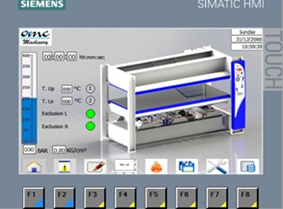
CE Compliance
All the presses produced by OMC comply with the EC Machinery Directive 2006/42/EC.
Customization
The following features can be customized according to customers’ needs:
• Platens dimensions;
• Maximum hydraulic pressure;
• Cylinder stroke;
• High temperatures (150°C – 180°C – 200°C – 250°C and above);
• Adjustable temperature in each platen;
• Fast closing / opening speed.
The following features can be added according to customers’ needs:
• Additional intermediate platens to get more daylights and increase production volumes;
• Sensors to check the parallel stroke of the pressing platen;
• Cylinder exclusion (automatic) + sensors to check the parallel stroke;
• Cylinder exclusion (manual);
• Power selector;
• Heat exchanger;
• Increased metal sheet thickness (5 mm instead of 3 mm) on the coils of the assembled plates for special applications;
• Ground and/or chromed surfaces of the solid steel platens for special applications;
• Interconnection between the press and the company IT system;
• Downstroke design (pressure from top to bottom)
• Special software to adjust temperature curves and download data file;
• Press without heating system, arranged to be used with customer’s own heating system;
• Linear transducers to adjust the opening, closing and slowing down of the pressing platen;
• Sensors to adjust the height of the platens;
• Special voltages;
• Non-EU standard requirements.