Edge and face gluing presses
Face gluing press 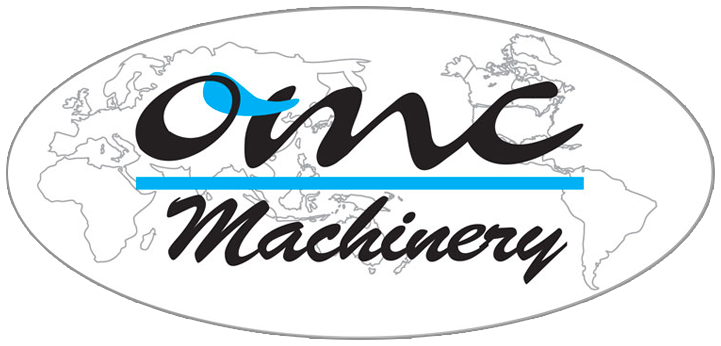
A “face gluing” press is designed to produce laminated timber by gluing slats/lamella with adhesive on the face of the workpiece; laminated beams are capable of providing high structural resistance, higher to that of solid wood.
Laminated timber is very stable and versatile and therefore particularly suitable for the construction industry; the work process of laminating also offers the opportunity to use multiple types of wood and therefore enhance the aesthetics of the product finishes.
Applications
- Production of window/door frames;
- Production of laminated beams for the construction industry.
Final products
- Window/door frames;
- laminated beams;
- Wide-span load-bearing beams;
- Trusses and roof structures.




PLs/TL
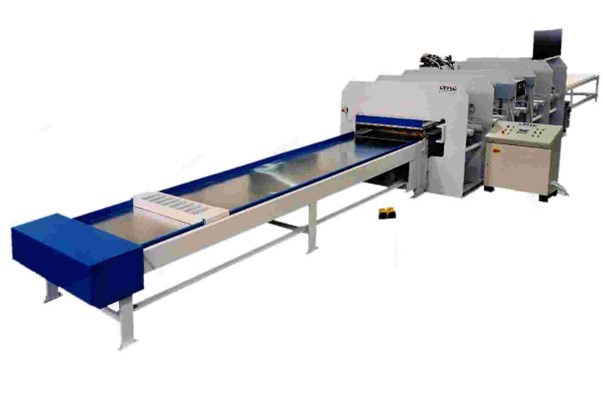
This press has been designed to produce laminated beams.
Models and loading system:
- PLs/TL-A (Maximum slat thickness 4 cm);
- PLs/TL-B (Maximum slat thickness 8 cm);
- PLs/TL-C (Maximum slat thickness 15 cm).
Manual loading on automatic loading system operated by pedal switch.
Unloading on idle roller table.
Useful dimensions and thrust
PLs/TL-A (Maximum slat thickness: 4 cm)
- 25/13: 2500×1300 mm, 10 Kg/cm2;
- 30/13: 3000×1300 mm, 10 Kg/cm2;
- 35/13: 3500×1300 mm, 10 Kg/cm2;
- 45/13: 4500×1300 mm, 10 Kg/cm2;
- 55/13: 5300×1300 mm, 10 Kg/cm2.
PLs/TL-B (Maximum slat thickness 8 cm)
- 25/13: 2500×1300 mm, 10 Kg/cm2;
- 30/13: 3000×1300 mm, 10 Kg/cm2;
- 35/13: 3500×1300 mm, 10 Kg/cm2;
- 45/13: 4500×1300 mm, 10 Kg/cm2;
- 55/13: 5300×1300 mm, 10 Kg/cm2.
PLs/TL-C (Maximum slat thickness 15 cm)
- 25/13: 2500×1300 mm, 10 Kg/cm2;
- 30/13: 3000×1300 mm, 10 Kg/cm2;
- 35/13: 3500×1300 mm, 10 Kg/cm2;
- 45/13: 4500×1300 mm, 10 Kg/cm2;
- 55/13: 5300×1300 mm, 10 Kg/cm2.
Standard equipment
- Structure made of oxy-cut steel sheets;
- Horizontal cylinders;
- Fixed stop bar to counter the thrust of the horizontal cylinders;
- Loading system with pusher;
- Unloading table with idle wheels;
- “Touch screen” digital panel + PLC;
- heating system with water/diathermic oil;
Accessories/Options
The PLS/TL presses can be equipped with the following accessories:
PLS CA model
- Automatic loading system (belt conveyor);
- Automatic glue spreader;
- Automatic composition system: the slats/lamellas /wood strips coming from the glue spreader are stopped and rotated 90° by a tilting device to form a pre-assembled group on a chain driven roller table . Each time a slat/lamella is added, the pre-assembled group goes down to make room for the next one, until the entire composition is completed.; the pre-assembled group of slats is then placed on the motorized roller conveyor to get into the press;
- High frequency generator;
- Platens fitted with plywood for high frequency;
- Motorized unloading system with transfer device.
PLs/TL CA
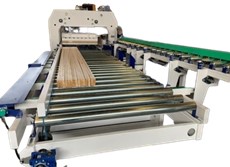
Automatic pressing line to produce laminated beams.
Loading/unloading systems:
- Automatic loading on conveyor belt activated by foot switch;
- Unloading on idle or motorized roller table.
Useful dimensions and hydraulic thrust
- 25/13: 2500×1300 mm, 10 Kg/cm2;
- 30/13: 3000×1300 mm, 10 Kg/cm2;
- 35/13: 3500×1300 mm, 10 Kg/cm2;
- 45/13: 4500×1300 mm, 10 Kg/cm2;
- 55/13: 5300×1300 mm, 10 Kg/cm2.
Standard equipment
- Structure made of oxy-cut steel sheets;
- Horizontal hydraulic cylinders;
- Fixed stop bar to counter the hydraulic thrust of the horizontal cylinders;
- Motorized belt system inside the press to receive and unload the workpieces;
- “Touch screen” digital control panel + PLC;
- heating system with water or diathermic oil.
Optionals / Accessories
- Automatic loading system (belt);
- Automatic glue spreader;
- Automatic lay up system: The slats/lamella coming from the glue spreader is stopped and rotated 90° by a tilting device to form a pre-assembled lamella group. Each time the operator adds one lamella, the pre-assembled group moves down for the thickness of one lamella, to make room for the next one, until the entire composition is completed; the pre-assembled group of slats is then placed on the motorized roller conveyor to get into the press;
- High Frequency generator;
- Multilayer platen for High Frequency;
- Motorized unloading system with transfer device.