PL Conversion Series 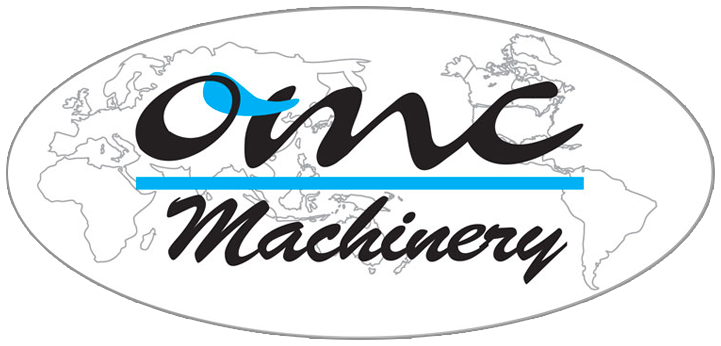
The “CONVERSION” presses use heat, air and vacuum to coat shaped workpieces with thermoforming films and veneer.
This series has been designed to achieve production volumes typically required by small and medium-sized companies.
Applications
- Coating of shaped surfaces with 3D thermoforming films (PVC, PPE, ABS etc.); this operation can be carried out with or without the membrane, depending on the case, (the press is equipped with a mechanical system that allows the operator to put on/take off the membrane very quickly);
- Coating of shaped surfaces with veneer (this operation always requires the use of the membrane).
Typical final products
- Various types of shaped panels;
- Doors, cabinet doors and flaps for bathrooms, kitchens etc.
Common features of PL Conversion models
Solid steel platens
Maximum working temperature: 250°C.
Maximum specific working pressure 30 kg/cm².
Our solid steel platens are manufactured in our own metal workshop with numerically controlled machines; the platens are made of steel plates drilled with holes for oil circulation;Types of heating systems
Oil boiler – maximum oil temperature: 120°C (customizable to higher temperatures)
Heating Fluid – Diathermic oil;Control panel
The press is equipped with a “touch screen” digital control panel;Compliance
The presses manufactured by OMC Machinery comply with the EC Machinery Directive 2006/42/EC.
Accessories/Options
Our PL Conversion presses can be equipped with the following accessories:
- PVC unwinding trolley with manual cutting system;
- PVC unwinding trolley with pneumatic cutting system;
- Partitioning bar for the loading system;
- JIG System 25/14 (magnetic);
- JIG System 30/14 (magnetic);
- JIG System 25/14 (electronic);
- JIG System 30/14 (electronic);
- Antistatic brush (1400 mm);
- System to process glossy PVC: intermediate flange, dedicated software and silicone membrane;
- Modular chamber h 90 mm;
- Modular chamber h 180 mm;
- Modular chamber h 180 mm;
- Surface cleaning system for glossy PVC;
- PVC granulator;
- PVC tensioning device;
- Tray scanning device with PVC tensioning and cutting system;
- Rotating stocking unit for 10 PVC rolls;
- Tilting unloading table with suction cup and motorized roller conveyor.










PL Conversion M
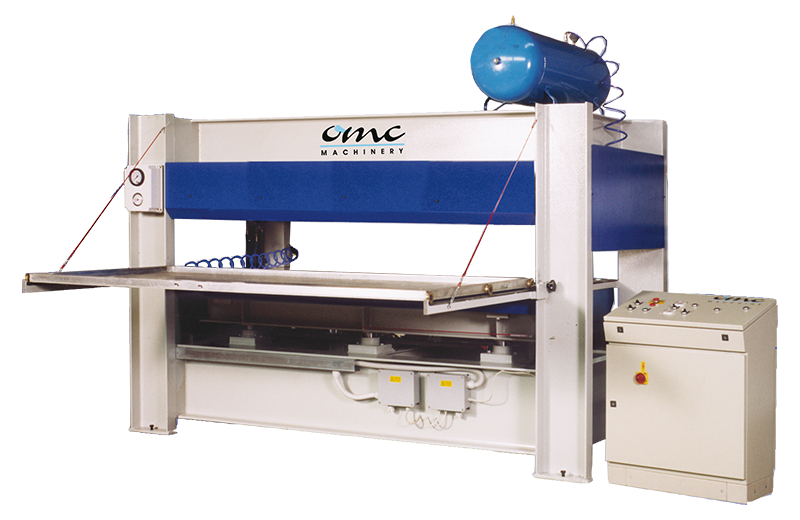
Applications:
Membrane press, equipped with No. 1 aluminum tray to coat one side of the workpieces with 3D thermoforming films and veneer.
Standard hot/cold press to coat workpieces with veneer and laminate.
Loading
MANUAL loading onto the long side.
Useful dimensions and thrust
- 25/13: 2350×1180 mm, 3,5 + 1 Kg/cm2;
- 30/13: 2800×1180 mm, 4 + 1 Kg/cm2:.
Standard equipment
- No. 1 rubber membrane;
- Heating system with diathermic oil heating;
- No. 1 vacuum pump.
PL Conversion CM and PL Conversion CA
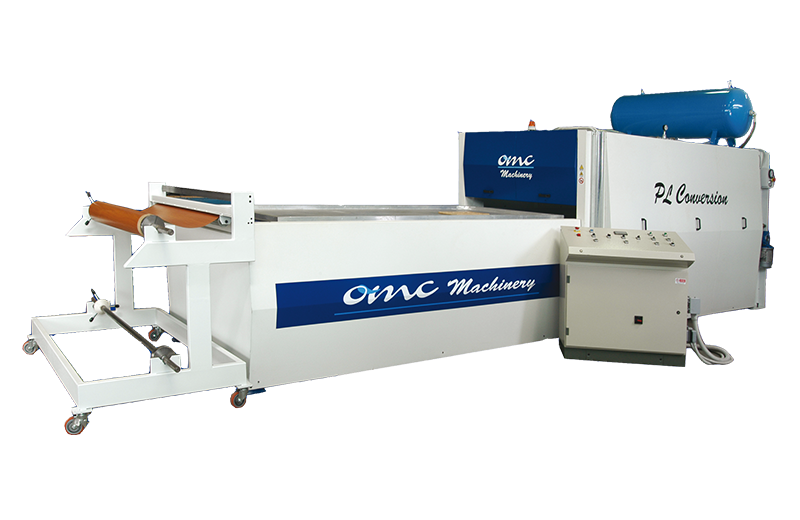
Applications:
This membrane press is equipped with aluminum tray/s to coat one side of the workpieces with 3D thermoforming films and veneer.
Models
Conversion CM:
MANUAL loading onto the short side
- Conversion CM 2V: this model is equipped with 2 manual trays.
Conversion CA:
AUTOMATIC loading onto the narrow side
- The Conversion CA model is equipped with 1 tray;
- The Conversion CA-2V model is equipped with 2 trays;
- The Conversion CA-3V model is equipped with 3 trays.
Useful dimensions and thrust
- 25/14: 2350×1280 mm, Kg/cm2 3,5 + 1;
- 30/14: 2850×1280 mm, Kg/cm2 4 + 1.
Standard equipment
- No. 1 rubber membrane;
- Heating system with diathermic oil;
- No. 1 vacuum pump;
- No. 1 500 litre air tank.


PL Conversion CM EXTRA and PL Conversion CA Extra
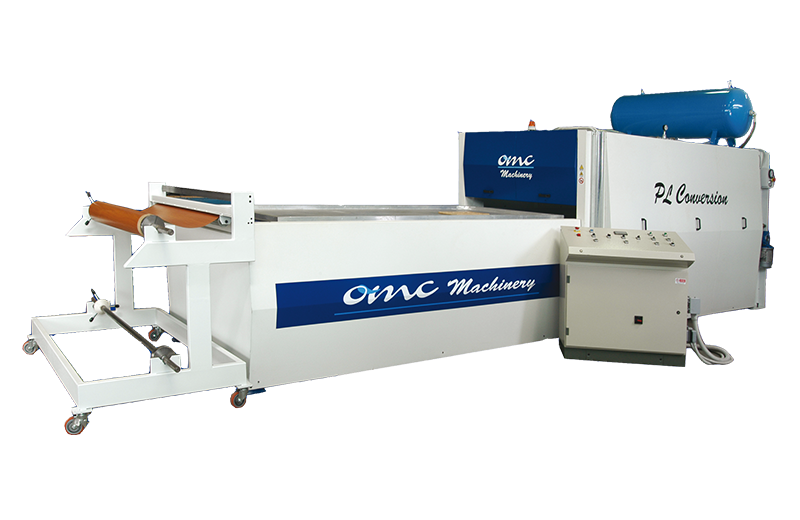
Applications:
This membrane press is equipped with aluminum tray/s to coat one side of the workpieces with 3D thermoforming films and veneer.
Models
Conversion CM Extra
MANUAL loading onto the short side
- Conversion CM Extra 2V: this model is equipped with 2 manual trays.
Conversion CA Extra:
AUTOMATIC loading onto the narrow side
- The Conversion CA Extra model is equipped with 1 tray;
- The Conversion CA Extra 2V model is equipped with 2 trays;
- The Conversion CA Extra 3V model is equipped with 3 trays.
Useful dimensions and thrust
- 25/14: 2350×1280 mm, Kg/cm2 6 + 1;
- 30/14: 2850×1280 mm, Kg/cm2 6 + 1.
Standard equipment
- No. 1 rubber membrane;
- Heating system with diathermic oil;
- No. 1 proportional control valve + 500 litre air tank;
- No. 1 vacuum pump with 500 litre tank.


PL Conversion S3 and PL Conversion S5
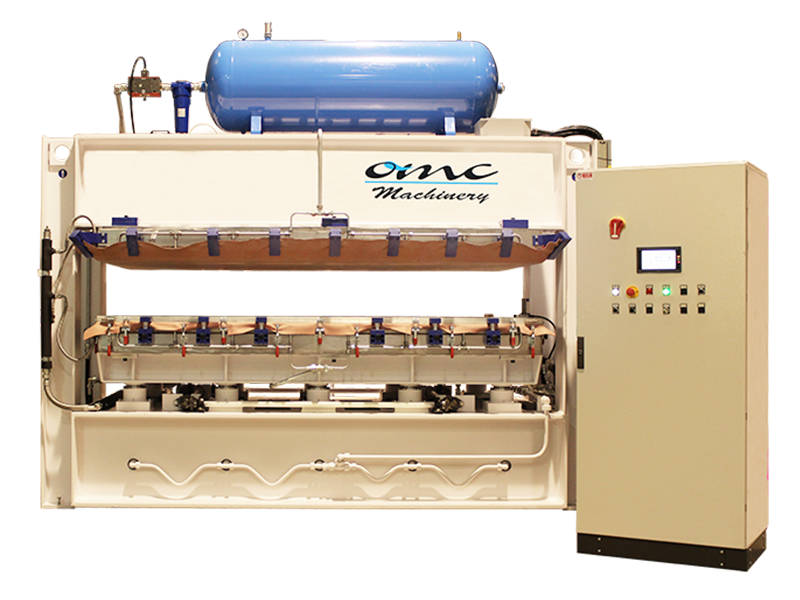
Applications:
These models are equipped with one or two membranes, to coat one or both sides of the workpieces with 3D thermoforming films or veneer.
These presses can also be used as standard heated/cold presses to coat workpieces with veneer and laminate.
Models
The press model “PL Conversion S3”, with manual loading, can be used in three different ways:
• As a Cold press;
• As a Heated press;
• As a membrane press to apply PVC and veneer on one side of the workpiece.
The “PL Conversion S5” model with manual loading, can be used in five different ways:
• As a Cold press;
• As a Heated press;
• As a membrane press to apply PVC and veneer on shaped surfaces on one side of the workpiece;
• As a membrane press to apply PVC and veneer on shaped surfaces on both sides of the workpiece;
• As a membrane press to apply glossy PVC thanks to the additional “high gloss system” (intermediate flange).
Useful dimensions and thrust
- 25/13: 2350×1180 mm, Kg/cm2 6 + 1;
- 30/13: 2850×1180 mm, Kg/cm2 6 + 1.
Standard equipment
S3 model:
• No. 1 rubber membrane;
• Heating system with diathermic oil;
• No. 1 proportional control valve + 500 litre air tank;
• No. 1 vacuum pump with 500 litre tank.
S5 model:
• No. 2 rubber membranes;
• Heating system with diathermic oil ;
• No. 2 proportional control valve + 500 litre air tank;
• No. 1 vacuum pump with 500 litre tank.

