Automatic loading/unloading systems, glue spreaders and bridges 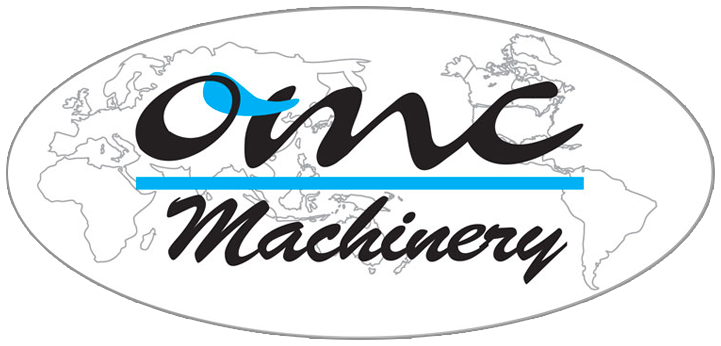
Suction cup bridge
The structure is made of thick tubulars.
Configuration: 1 loading and 1 unloading unit;
The X and Y-axes are activated by a motor with reducer and controlled by an inverter and an encoder that allow to achieve maximum precision.
The motion of the axes is achieved by a motorized belt system and linear recirculating ball guides.
The suction cup bridge system is controlled by a PLC (Programmable Logic Controller): the operator can enter the process parameters in a “Touch Screen” display. The string of parameters can be saved and retrieved in the “recipe” digital page.

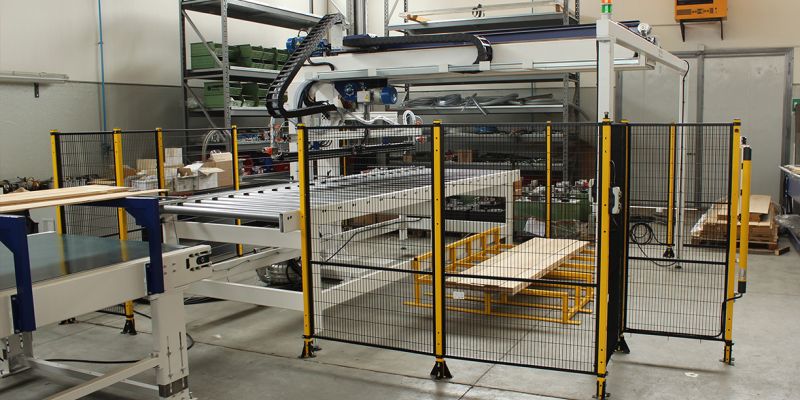
Pusher on lifting platform
The hydraulic lifting platform, manufactured by OMC, automatically rises to working level after each loading, so that the pneumatic pusher can push the top panel of the stack into the following station (e.g. brushing / gluing machine etc.).
The electro-pneumatic pusher, manufactured by OMC, can load panels of any thickness, down to a minimum of 10 mm, into the following station (brushing or gluing machine). Panels with a thickness of less than 10 mm will be pushed by a suction cups system.
Disc conveyor
The disc conveyor (motorized or idle), manufactured by OMC, receives the panels from the gluing machine. The thin discs minimize the contact surface with the layer of glue of the panels.
Standard equipment
- The structure is made of welded steel profiles, and it is adjustable in height to compensate for uneven floors;
- The discs dip into the water inside a tank made of galvanized sheet: this allows for self-cleaning and avoids the need for daily washing;
- The discs are made of stainless steel to prevent glue residues.
Storage station for coating materials
Fixed station
A storage station with shelves can be installed on top of the disc conveyor to stock the coating materials (veneer, laminate etc.).
The operator can manually pick up the coating material to be placed under/on top of the panel on the loading belt of the next station.
Motorized station
A motorized storage station with foot switch can be installed beside the loading belt: the operator activates the forward/backward movement of the shelves that move above the loading table towards the operator who can easily pick up the coating material and place it on the belt.
Loading table
The structure of the loading table is made of welded steel profiles, and it is adjustable in height to compensate for uneven floors.
The PVC belt allows easy cleaning from residues of two-component polyurethane glues.
The table is equipped with a system for adjusting the centering and tensioning of the belt.
The belt is activated by a foot switch.
The motorization of the belt is controlled by a variable speed motor with adjustable speed via inverter.
Positioner
The positioner takes the panel coming out of the gluing machine and places it with the right alignment on top of the coating material (veneer / laminate) previously placed by the operator on the loading belt.
Automatic chain positioner
The disc-holder bars emerge from under the lay-up table to take and bring the panel onto the loading belt. The bars then return to their initial position and the panel is stopped in the desired position by a stop bar.
Automatic positioner with sliding carriage
A vice driven by pneumatic cylinders grabs the panel, drags it over the loading table and drops it gently on the the loading belt.
Manual positioner with sliding carriage
A vice driven by pneumatic cylinders locks the panel and the operator pushes the slide carriage along the loading table and lets the panel drop down gently in the desired position.
Unloading system
Unloading table with idle wheels
When the pressing cycle is finished, the panels are pushed out of the press by the rotation of the belt system onto the unloading table with idle wheels.
The sliding of the panel on the idle wheels occurs due to gravity.
The structure of the unloading table is made of welded steel profiles, and it is adjustable in height to compensate for uneven floors.
Motorized roller table
The panels automatically exit the press onto the motorized roller table at the end of the pressing cycle.
The motorized rollers can transfer the pressed panels to the next station.
The structure of the loading table is made of welded steel profiles, and it is adjustable in height to compensate for any possible unevenness of the floor.
Automatic stacker
The automatic stacker piles up the panels at the end of the line. The belt system lays down the panel and then lifts up automatically to place the next panel on top of the pile.